Technology
UT Dallas Researchers Create Low-Cost ‘Artificial Muscles’ That Could Power the Future of Smart Clothing and Robotics » Dallas Innovates
Mengmeng Zhang, left, a research scientist at UT Dallas’ NanoTech Institute and lead author of the study, wears a U.S. Olympic team jacket embedded with artificial muscles created using an earlier, mandrel-wrapped process. At right is Ray Baughman, director of the NanoTech Institute. [Photo: UTD] Researchers at UT Dallas’ NanoTech Institute have developed a low-cost […]
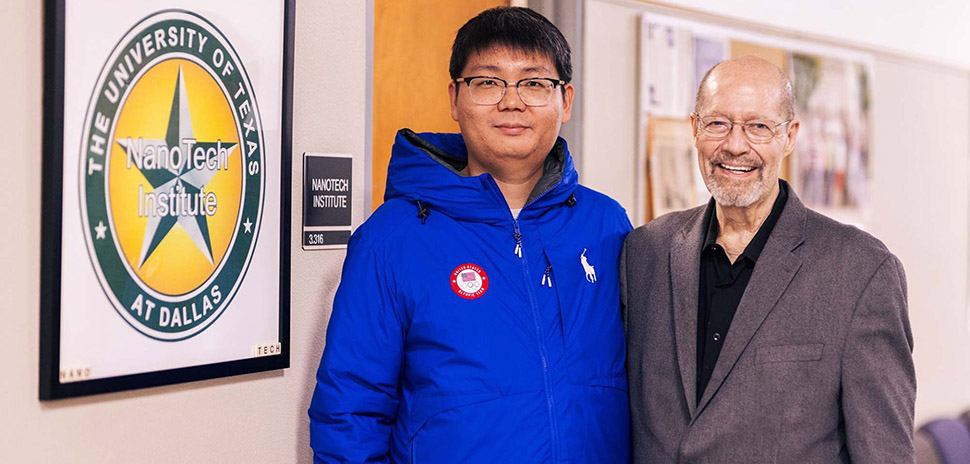
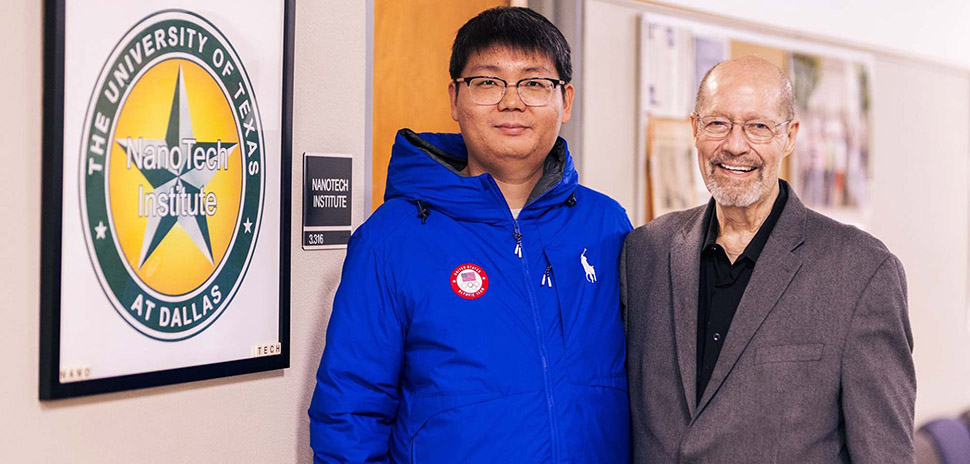
Mengmeng Zhang, left, a research scientist at UT Dallas’ NanoTech Institute and lead author of the study, wears a U.S. Olympic team jacket embedded with artificial muscles created using an earlier, mandrel-wrapped process. At right is Ray Baughman, director of the NanoTech Institute. [Photo: UTD]
Researchers at UT Dallas’ NanoTech Institute have developed a low-cost method to fabricate artificial muscles that could open new doors for robotics, energy harvesting, and smart clothing.
But these “muscles” aren’t biological—they’re engineered fibers that behave something like them. When triggered by heat or electricity, the fibers contract, expand, or twist, producing motion without motors.
In this case, polymer yarns are a type of smart material that respond to temperature changes. The UT Dallas team’s advance could move this lab innovation closer to real-world use in clothing, robotics, and other systems that need quiet, energy-efficient movement.
In a study published March 7 in Science, the team describes a mandrel-free technique for making the springlike, thermally driven polymer muscles that can stretch up to 97% of their original length and achieve a spring index over 50.
“High-spring-index yarns can be made much less expensively by this mandrel-free method,” said Dr. Mengmeng Zhang, a research scientist at UT Dallas’ Alan G. MacDiarmid NanoTech Institute and lead author of the study. “When heated and cooled, these muscles can significantly contract and elongate due to their large spring index.”
Mandrel-free-fabricated coiled polymer fibers: Springs with a small spring index are tightly wound and stiffer than those with a higher index, which are more loosely wound and more flexible, such as a Slinky toy. Individual fiber diameter is 0.28 millimeters.
[Photo: UTD]
Innovation enables movement without motors
Traditionally, high-spring-index artificial muscles are made by wrapping fibers around a mandrel, then dissolving it—a costly process that wastes materials. The new method eliminates the mandrel altogether.
“The problem has been that there are no process reports for making mandrel-free, large-spring-index yarns other than to dissolve the mandrel after muscle coiling, which wastes the large-diameter polymer fiber that is typically used as a mandrel and creates a waste stream,” said Dr. Ray Baughman, senior and co-corresponding author and director of the NanoTech Institute.
Using dynamic covalent chemistry, the team created fibers that twist and ply themselves into springlike coils—each fiber acting as a mandrel for another. The resulting artificial muscles vary in stiffness and flexibility and can be tuned for different uses.
The research was funded by the Office of Naval Research, the Air Force Office of Scientific Research, and The Welch Foundation.
From Olympic jackets to energy harvesters
The same team previously licensed mandrel-wrapped artificial muscle technology to a clothing manufacturer, which integrated the fibers into jackets worn by the U.S. team during the 2022 Winter Olympics. But the process was too costly for commercial rollout.
“Our new mandrel-free method for making high-spring-index coiled fiber avoids this major problem, so it may soon enable the commercialization of new comfort-adjusting jackets,” Baughman said.
Beyond clothing, the muscles could be used in devices that harvest mechanical energy or function as self-powered strain sensors. Zhang said the method even allows for variable spring indexes along a single fiber, enhancing adaptability.
The strokes of contraction and expansion are heat-driven, either through electricity, solvents, or electrochemical methods.
Broad team
Other co-authors include:
-
Dr. Shaoli Fang, associate research professor and co-corresponding author
-
Chemistry doctoral student Ishara Ekanayake
-
Former researchers Dr. Jiyoung Oh and Zhong Wang (PhD ’21)
-
Researchers from Texas State University, Tekirdağ Namık Kemal University, and Lintec of America
The team has applied for a patent on the technology.
Don’t miss what’s next. Subscribe to Dallas Innovates.
Track Dallas-Fort Worth’s business and innovation landscape with our curated news in your inbox Tuesday-Thursday.